About our flanges
Flanges general information
The use of flanges, as a pipe connection element, is generally imposed by the need for assembly and disassembly of equipment or pipe parts.
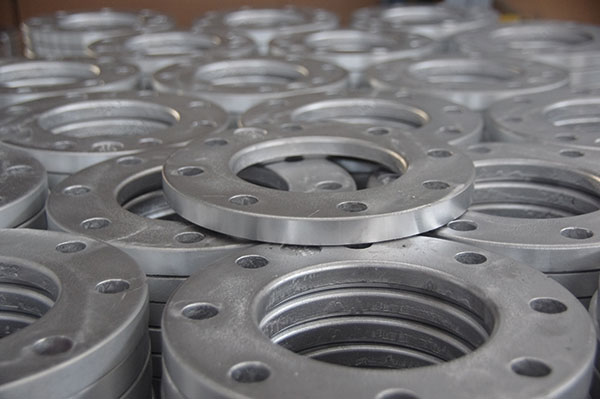
LOOSE FLANGES
The loose flanges are slipped onto the pipe and rest against a ring or collar welded to the pipe, which is the only part of the joint that is in contact with the fluid. Their use is economical for aggressive fluids that require piping made of expensive materials (stainless steel, etc.) since the flanges can be made of less valuable materials such as aluminium, carbon steel or other.
Usually the aluminium flanges are supplied with blank surfaces and, without any treatment, are installed on stainless steel or aluminium or plastic pipes as, in normal atmosphere, the natural film of aluminium oxide (Al2O3) that forms on the flange surface shows a sufficient resistance to corrosion.
In humid atmosphere it forms a thick layer of oxide whose outside is porous and hydrates with small particles or white deposits, while the side adherent to the surface is a continuous porous film durable and insoluble in 4.5 to 8 ph field.
This natural passivation allows, in most cases, to use aluminium flanges with blank surfaces. On the surface of contact between stainless steel and aluminium is not produced any phenomenon of corrosion for contact.
Temperature | from -250°C up to 50°C | 100 °C | 150 °C |
Tensile strength N/mm2 | 170 | 150 | 120 |
Our aluminium flanges follows the dimensions according to the UNI EN 1092-1:2013 PN10, PN16, EN1759-4 Class 150 (ANSI TYPE) and DIN 16963 (TP-TYPE) regarding both the outer diameter of the flanges and the interaxis space number of the holes for the bolts. These dimensions apply with the UNI 2223-67 6092-67, DIN 2501 and DIN 2527 norms.
Thickness: over ND 25 up to ND 250 according to UNI 6089 (DIN 2642) standards, over ND 250 see the dimensional tables. For the thickness of the TP-TYPE flanges (strengthened and reg. form) see the relative dimensional tables.
Tests carried out from official corporations at our factory attest, for flanges of our production (ISO and METRIC flanges up to DN 500 and LITE flanges) the tightness up to 10 or 16 bar and various tests from our quality service attest the tightness of TP-TYPE flanges (hydrostatic test up to ND 300).
As information from DN 500 the maximum allowable pressure changes from 6 to 4 bar.
The practical use of millions of gea flanges for several years and a business system of production technology certified by the prestigious ISO 9001:2015 demostrate that our aluminium flanges afford an absolutely reliability.
Type of coating | EPOXI-POLYESTER |
Composition | Epoxi-polyester powders |
Mechanical properties of the coating | |
Thickness (ISO 2360) | 60 micron |
Adherence (ISO 2409) | GT 0 |
Hardness (EN ISO 2815) | > 90 |
Collision Resistance (ECCA T8) | > 2,5 Nm |
Shaping (ISO 1520) | > 3 mm |
Bending (ISO 1519) | 5 mm |
Brightness | 80 – 90 glos |
Resistance to corrosion | |
Saline fog (ASTM B117) | 500 hours (1 mm. of penetration on the cross) |
Humidity resistance (IUNI 8744) | 500 hours: no change |
Demineralized water (ASTM D870) | 500 hours: no change |
Resistance to solvents | |
Ethyl alcohol – Buthyl alcoh | No softening |
Toluene – Xylene | Light softening |
Trichloroetane – Perchloroetane | Hard softening |
Methylethylketone – Acetone | Hard softening |
Gasoline | No softening |
– Temperature of use: from -25°C to 50°C
– Standard colour: RAL 7031